1. Prueba teórica y análisis
De los 3válvulas de neumáticosmuestras proporcionadas por la empresa, 2 son válvulas y 1 es una válvula que aún no se ha utilizado. Para A y B, la válvula que no se ha utilizado está marcada en gris. Figura completa 1. La superficie exterior de la válvula A es poco profunda, la superficie exterior de la válvula B es la superficie, la superficie exterior de la válvula C es la superficie y la superficie exterior de la válvula C es la superficie. Las válvulas A y B están cubiertas de productos de corrosión. Las válvulas A y B están agrietadas en las curvas, la parte exterior de la curva está a lo largo de la válvula, la boca del anillo de la válvula B está agrietada hacia el final y la flecha blanca entre las superficies agrietadas en la superficie de la válvula A está marcada. De lo anterior, las grietas están por todas partes, las grietas son las más grandes y las grietas están por todas partes.
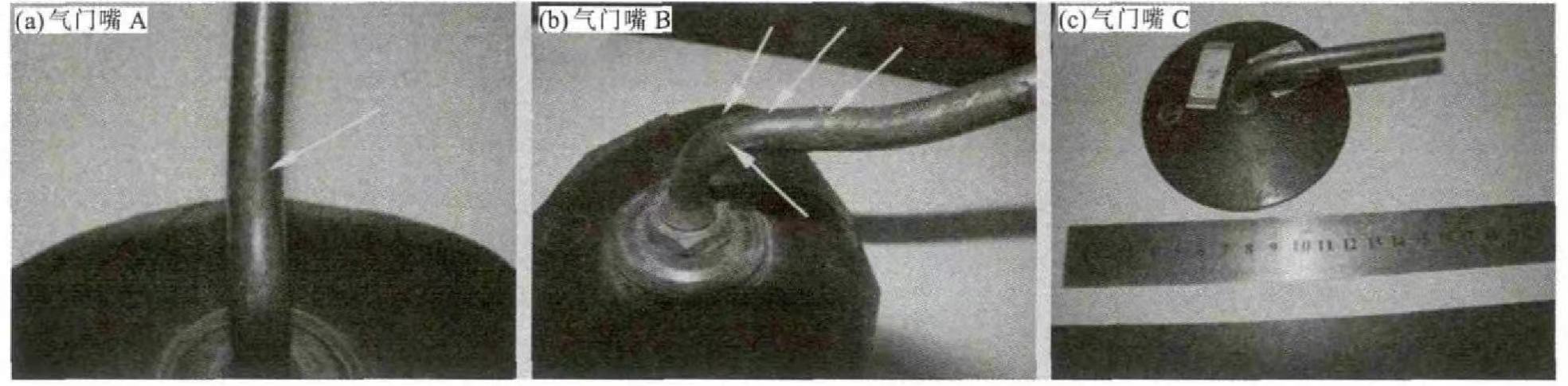
Una sección de laválvula de neumáticoLas muestras A, B y C se cortaron de la curva, se observó la morfología superficial con un microscopio electrónico de barrido ZEISS-SUPRA55 y se analizó la composición de microáreas mediante EDS. La Figura 2 (a) muestra la microestructura de la superficie de la válvula B. Se observa una gran cantidad de partículas blancas y brillantes en la superficie (indicadas por las flechas blancas en la figura), y el análisis EDS de las partículas blancas muestra un alto contenido de S. Los resultados del análisis del espectro de energía de las partículas blancas se muestran en la Figura 2 (b).
Las figuras 2 (c) y (e) son las microestructuras superficiales de la válvula B. Se puede ver en la figura 2 (c) que la superficie está casi completamente cubierta por productos de corrosión, y los elementos corrosivos de los productos de corrosión por análisis del espectro de energía incluyen principalmente S, Cl y O, el contenido de S en posiciones individuales es mayor, y los resultados del análisis del espectro de energía se muestran en la figura 2 (d). Se puede ver en la figura 2 (e) que hay microfisuras a lo largo del anillo de la válvula en la superficie de la válvula A. Las figuras 2 (f) y (g) son las micromorfologías superficiales de la válvula C, la superficie también está completamente cubierta por productos de corrosión, y los elementos corrosivos también incluyen S, Cl y O, similar a la figura 2 (e). La razón del agrietamiento puede ser el agrietamiento por corrosión bajo tensión (SCC) del análisis del producto de corrosión en la superficie de la válvula. La figura 2(h) muestra también la microestructura superficial de la válvula C. Se observa que la superficie está relativamente limpia y que su composición química, analizada por EDS, es similar a la de la aleación de cobre, lo que indica que la válvula no presenta corrosión. Al comparar la morfología microscópica y la composición química de las tres superficies de la válvula, se observa la presencia de medios corrosivos como S, O y Cl en el entorno circundante.
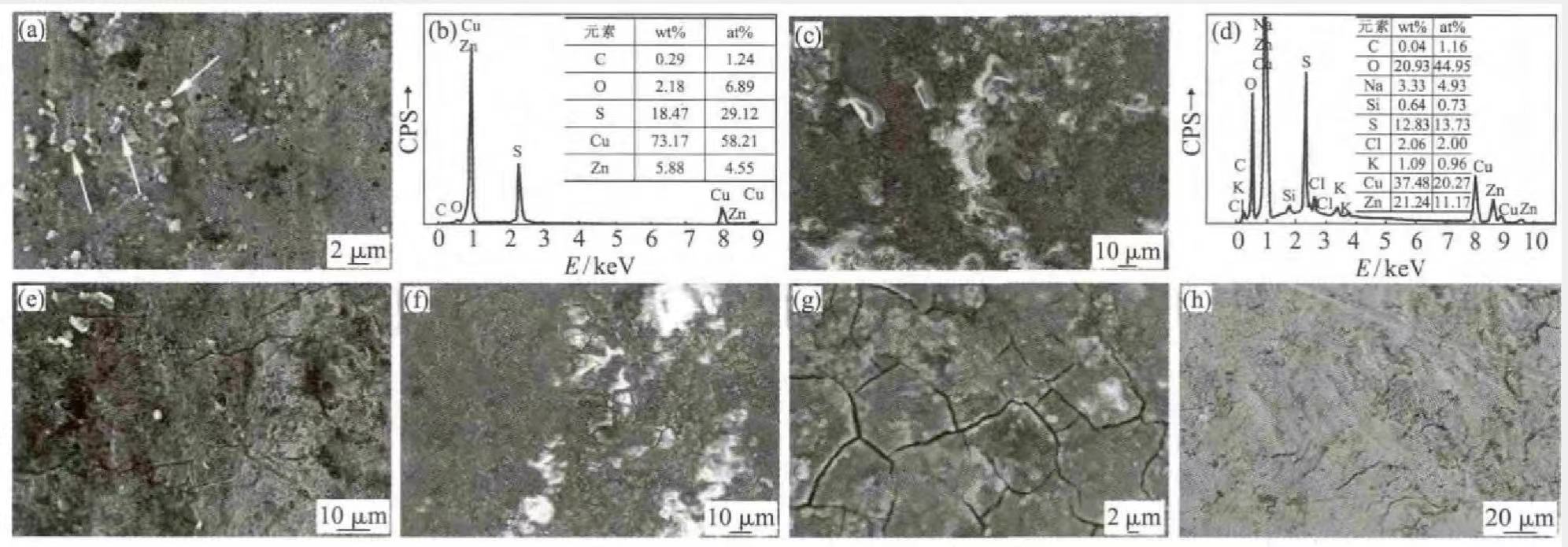
La grieta de la válvula B se abrió mediante una prueba de flexión, y se observó que no penetraba toda la sección transversal de la válvula, se agrietaba en el lado de la curvatura hacia atrás y no en el lado opuesto. La inspección visual de la fractura muestra un color oscuro, lo que indica corrosión, y algunas partes de la fractura son oscuras, lo que indica que la corrosión es más grave en estas zonas. La fractura de la válvula B se observó con un microscopio electrónico de barrido, como se muestra en la Figura 3. La Figura 3 (a) muestra el aspecto macroscópico de la fractura de la válvula B. Se puede observar que la fractura externa cerca de la válvula está cubierta por productos de corrosión, lo que indica nuevamente la presencia de medios corrosivos en el entorno circundante. Según el análisis del espectro de energía, los componentes químicos del producto de corrosión son principalmente S, Cl y O, con un contenido relativamente alto de S y O, como se muestra en la Figura 3 (b). Al observar la superficie de la fractura, se observa que el patrón de crecimiento de la grieta es de tipo cristalino. También se puede observar un gran número de grietas secundarias al observar la fractura a mayor aumento, como se muestra en la Figura 3(c). Las grietas secundarias están marcadas con flechas blancas en la figura. Los productos de corrosión y los patrones de crecimiento de grietas en la superficie de la fractura muestran nuevamente las características del agrietamiento por corrosión bajo tensión.
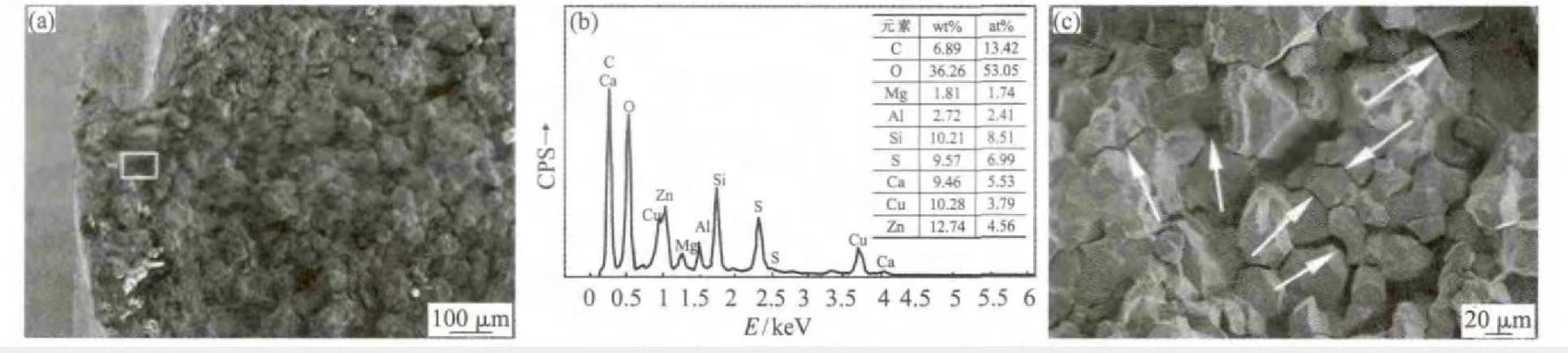
La fractura de la válvula A no se ha abierto, retire una sección de la válvula (incluyendo la posición agrietada), esmerile y pula la sección axial de la válvula y use una solución de Fe Cl3 (5 g) + HCl (50 mL) + C2H5OH (100 mL) para grabarla, y la estructura metalográfica y la morfología del crecimiento de la grieta se observaron con el microscopio óptico Zeiss Axio Observer A1m. La Figura 4 (a) muestra la estructura metalográfica de la válvula, que es una estructura de fase dual α+β, y β es relativamente fino y granular y se distribuye en la matriz de fase α. Los patrones de propagación de grietas en las grietas circunferenciales se muestran en la Figura 4(a), (b). Dado que las superficies de la grieta están llenas de productos de corrosión, el espacio entre las dos superficies de la grieta es amplio y es difícil distinguir los patrones de propagación de la grieta. fenómeno de bifurcación. También se observaron muchas grietas secundarias (marcadas con flechas blancas en la figura) en esta grieta primaria, véase la Fig. 4(c), y estas grietas secundarias se propagaron a lo largo de la veta. La muestra de válvula grabada se observó por SEM, y se encontró que había muchas microgrietas en otras posiciones paralelas a la grieta principal. Estas microgrietas se originaron en la superficie y se expandieron al interior de la válvula. Las grietas tenían bifurcación y se extendían a lo largo de la veta, véanse las Figuras 4 (c), (d). El entorno y el estado de tensión de estas microgrietas son casi los mismos que los de la grieta principal, por lo que se puede inferir que la forma de propagación de la grieta principal también es intergranular, lo que también se confirma mediante la observación de la fractura de la válvula B. El fenómeno de bifurcación de la grieta muestra nuevamente las características del agrietamiento por corrosión bajo tensión de la válvula.
2. Análisis y discusión
En resumen, se puede inferir que el daño de la válvula se debe a la corrosión bajo tensión causada por SO₂. La corrosión bajo tensión generalmente requiere tres condiciones: (1) materiales sensibles a la corrosión bajo tensión; (2) medio corrosivo sensible a las aleaciones de cobre; (3) ciertas condiciones de tensión.
Se cree generalmente que los metales puros no sufren corrosión bajo tensión, y todas las aleaciones son susceptibles a ella en diversos grados. En el caso de los materiales de latón, se cree generalmente que la estructura bifásica presenta mayor susceptibilidad a la corrosión bajo tensión que la estructura monofásica. Se ha reportado en la literatura que cuando el contenido de Zn en el latón supera el 20%, presenta mayor susceptibilidad a la corrosión bajo tensión, y cuanto mayor sea el contenido de Zn, mayor será la susceptibilidad a la corrosión bajo tensión. La estructura metalográfica de la boquilla de gas en este caso es una aleación bifásica α+β, y el contenido de Zn es de aproximadamente el 35%, muy superior al 20%, por lo que presenta una alta sensibilidad a la corrosión bajo tensión y cumple con las condiciones del material requeridas para el agrietamiento por corrosión bajo tensión.
En materiales de latón, si no se realiza un recocido de alivio de tensiones después de la deformación por trabajo en frío, se producirá corrosión bajo tensión en condiciones de tensión adecuadas y entornos corrosivos. La tensión que causa el agrietamiento por corrosión bajo tensión suele ser una tensión de tracción local, que puede ser tensión aplicada o tensión residual. Tras inflar un neumático de camión, se genera tensión de tracción a lo largo del eje de la boquilla de aire debido a la alta presión en el neumático, lo que provoca grietas circunferenciales en la boquilla. La tensión de tracción causada por la presión interna del neumático se puede calcular simplemente mediante σ = p R/2t (donde p es la presión interna del neumático, R es el diámetro interior de la válvula y t es el espesor de la pared de la válvula). Sin embargo, en general, la tensión de tracción generada por la presión interna del neumático no es demasiado grande, por lo que se debe considerar el efecto de la tensión residual. Las posiciones de agrietamiento de las boquillas de gas se encuentran todas en la curvatura posterior, y es evidente que la deformación residual en la curvatura posterior es grande y existe una tensión de tracción residual en esa zona. De hecho, en muchos componentes prácticos de aleación de cobre, la corrosión bajo tensión rara vez se debe a tensiones de diseño, y la mayoría se debe a tensiones residuales que pasan desapercibidas e ignoradas. En este caso, en la curva posterior de la válvula, la dirección de la tensión de tracción generada por la presión interna del neumático coincide con la dirección de la tensión residual, y la superposición de estas dos tensiones proporciona la condición de tensión para el SCC.
3. Conclusión y sugerencias
Conclusión:
El agrietamiento de laválvula de neumáticoSe produce principalmente por el agrietamiento por corrosión bajo tensión provocado por SO2.
Sugerencia
(1) Rastrear la fuente del medio corrosivo en el entorno que rodea alválvula de neumáticoEvite el contacto directo con el medio corrosivo circundante. Por ejemplo, puede aplicar una capa de recubrimiento anticorrosivo a la superficie de la válvula.
(2) La tensión de tracción residual del trabajo en frío se puede eliminar mediante procesos apropiados, como el recocido de alivio de tensión después del doblado.
Hora de publicación: 23 de septiembre de 2022